Die casting has become an essential manufacturing process in Malaysia, contributing significantly to the country’s industrial growth. The process, which involves forcing molten metal into a mold under high pressure to create detailed and precise components, has revolutionized the way industries produce parts for a wide range of applications. With its ability to produce complex and durable components quickly and efficiently, die casting has become a favored technique for sectors like automotive, electronics, and aerospace. In Malaysia, die casting has become integral to the manufacturing landscape, helping local industries meet both domestic and international demand for high-quality metal parts. As technology continues to evolve, die casting remains a key player in Malaysia’s efforts to stay competitive in the global manufacturing sector.
One of the main advantages of die casting in Malaysia is its ability to produce parts with exceptional precision and consistency. The process is capable of producing parts with tight tolerances, complex geometries, and smooth finishes, all of which are crucial in industries where performance and quality are paramount. This is particularly important in the automotive sector, where die-cast components are used in engine blocks, transmission housings, and structural parts. By allowing manufacturers to achieve high levels of detail and accuracy, die casting has become a trusted method for producing parts that must meet rigorous standards. The precision offered by die casting not only improves the quality of the final product but also minimizes the need for additional machining, which can save time and reduce production costs.
Another reason for the growing adoption of die casting in Malaysia is the material versatility it offers. The process can be used with a wide range of metals, including aluminum, zinc, magnesium, and copper alloys, which each have distinct properties suited to different applications. Aluminum die casting, for instance, is widely used in the automotive industry due to the metal’s lightweight and durable characteristics. Zinc die casting, on the other hand, is often favored for producing smaller, more intricate parts, especially in the electronics and consumer products sectors. This flexibility allows manufacturers in Malaysia to tailor their production to the specific needs of their industry, providing customized solutions that optimize both performance and cost.
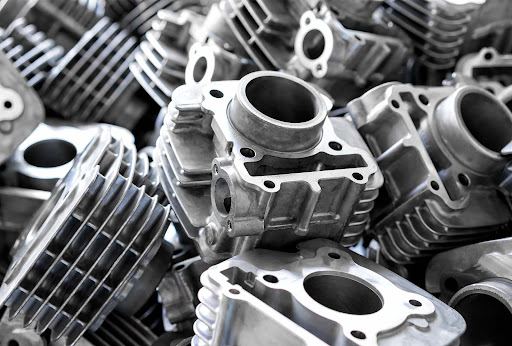
The speed and efficiency of the powder coating malaysia process make it highly attractive to Malaysian manufacturers, particularly in industries where high-volume production is essential. The ability to produce large quantities of parts in a relatively short amount of time makes die casting an ideal solution for mass production. Once the mold is created, it can be used repeatedly to produce thousands of identical parts, reducing lead times and increasing output. This is particularly beneficial in sectors like automotive manufacturing, where components are needed in large volumes to meet global production demands. Furthermore, die casting requires fewer post-production steps, such as machining or finishing, which contributes to its cost-effectiveness. As Malaysia’s manufacturing industry continues to grow, the speed and efficiency of die casting ensure that companies remain competitive on both a national and international scale.
Despite its many benefits, die casting in Malaysia faces challenges related to environmental sustainability and resource management. The process involves the use of molten metals, which can generate waste, emissions, and other byproducts that may have an environmental impact. As a result, there is growing pressure on manufacturers to adopt more sustainable practices and reduce the environmental footprint of their operations. Many die casting companies in Malaysia are responding to this challenge by implementing energy-efficient technologies, recycling metal scrap, and using environmentally friendly materials. By focusing on sustainability, these companies are not only reducing their environmental impact but also improving their long-term viability in an increasingly eco-conscious market.
In conclusion, die casting has become a vital part of Malaysia’s manufacturing industry, driving innovation and efficiency in several key sectors. The process’s precision, material versatility, and efficiency have made it indispensable for industries such as automotive, aerospace, and electronics. As Malaysia continues to focus on maintaining high production standards, die casting remains an essential tool in meeting the demands of global markets. The ongoing investment in sustainable practices and cutting-edge technologies ensures that die casting in Malaysia will remain competitive, eco-friendly, and able to meet the evolving needs of both local and international industries. With its ability to produce high-quality, cost-effective parts quickly and accurately, die casting will continue to play a key role in shaping the future of manufacturing in Malaysia.